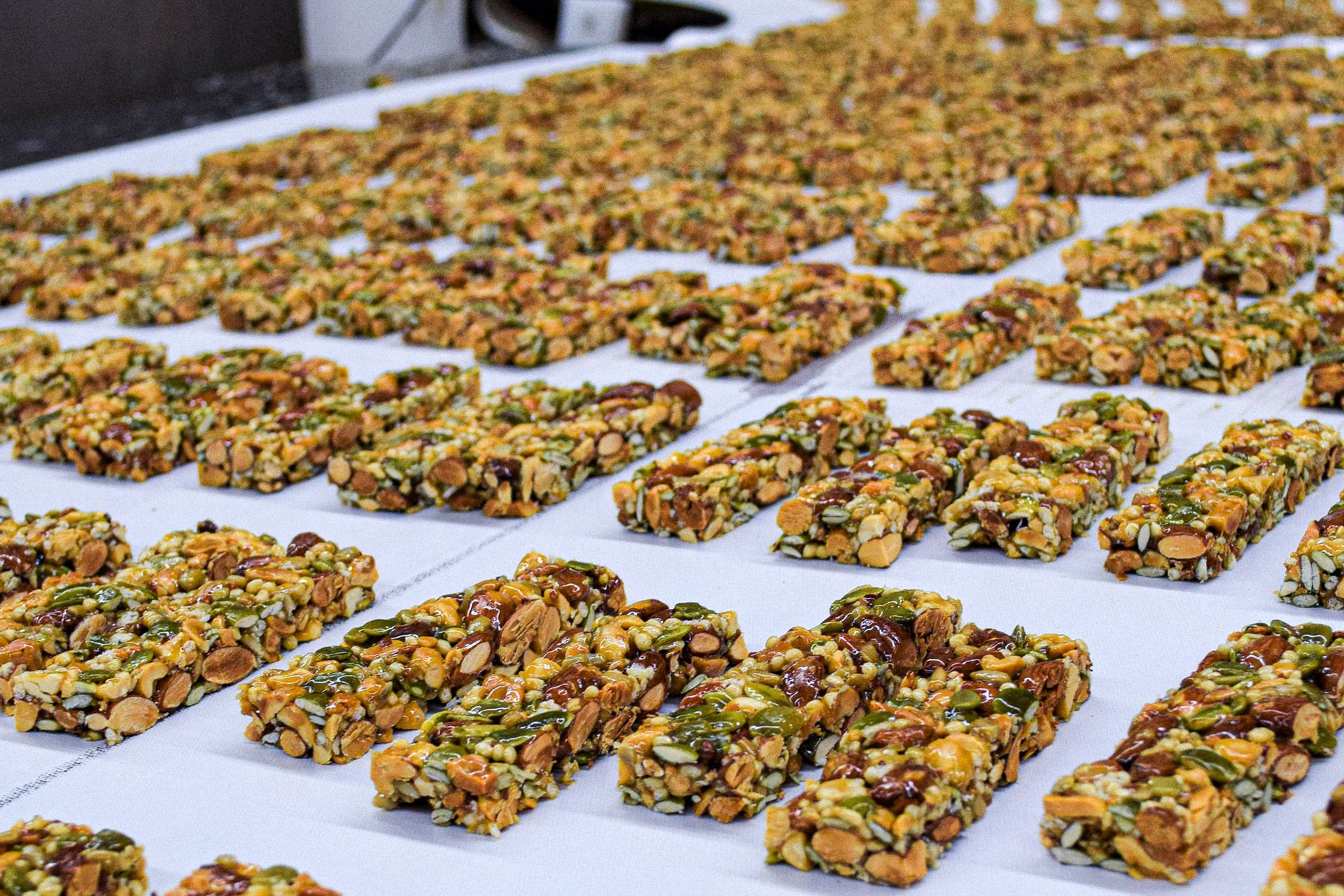
Facilities
Located roughly 25 miles from Syracuse and in close proximity to two major interstate routes, our State-of-the-Art Cato, NY, production facility offers customers everything they need from their bar manufacturer: Consistent, on-time production and turnarounds, strict adherence to brand standards and confidentiality, and outstanding customer service.
Production Capacity
Facility Size:
65,000
sq. ft.
Optimum Shift Capacity:
200,000
bars per shift
Maximum Estimated Annual Production:
300
million bars
Location
Our location is ideally situated for all your production needs, with easy access to major interstates to ensure timely delivery to any destination.
12351 NY-34, Cato, NY 13033
State-of the-Art Production Lines
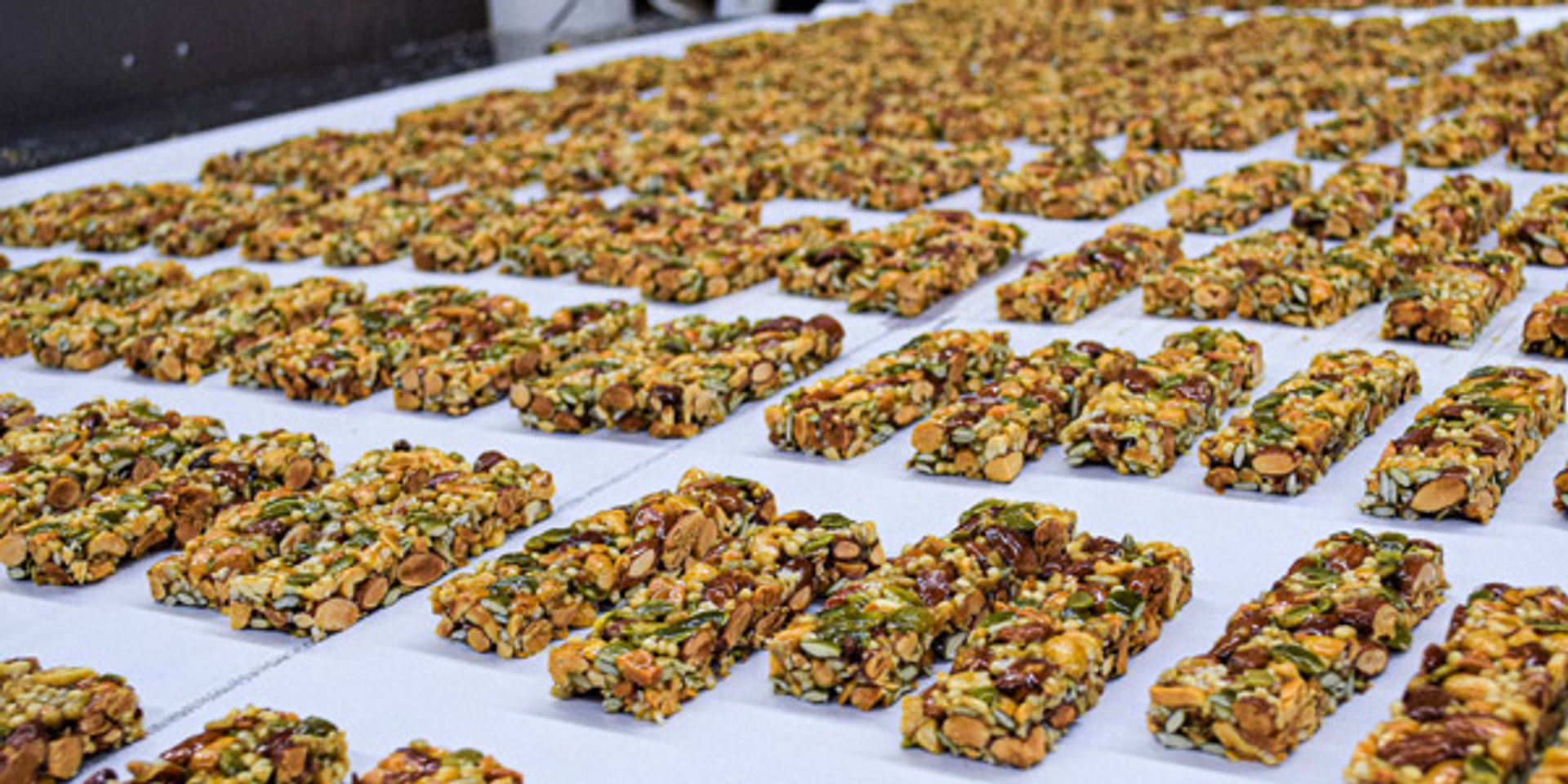
Extrusion Line
Our carefully controlled extrusion method creates a highly compressed bar suitable for high protein or high nutrition bar varieties. Compression rollers force the product through a die, forming rows of “ropes” or “ribbons” onto a conveyor belt. The width of the “ropes” is determined by the die used. The product is then cut into the length specified by the customer.
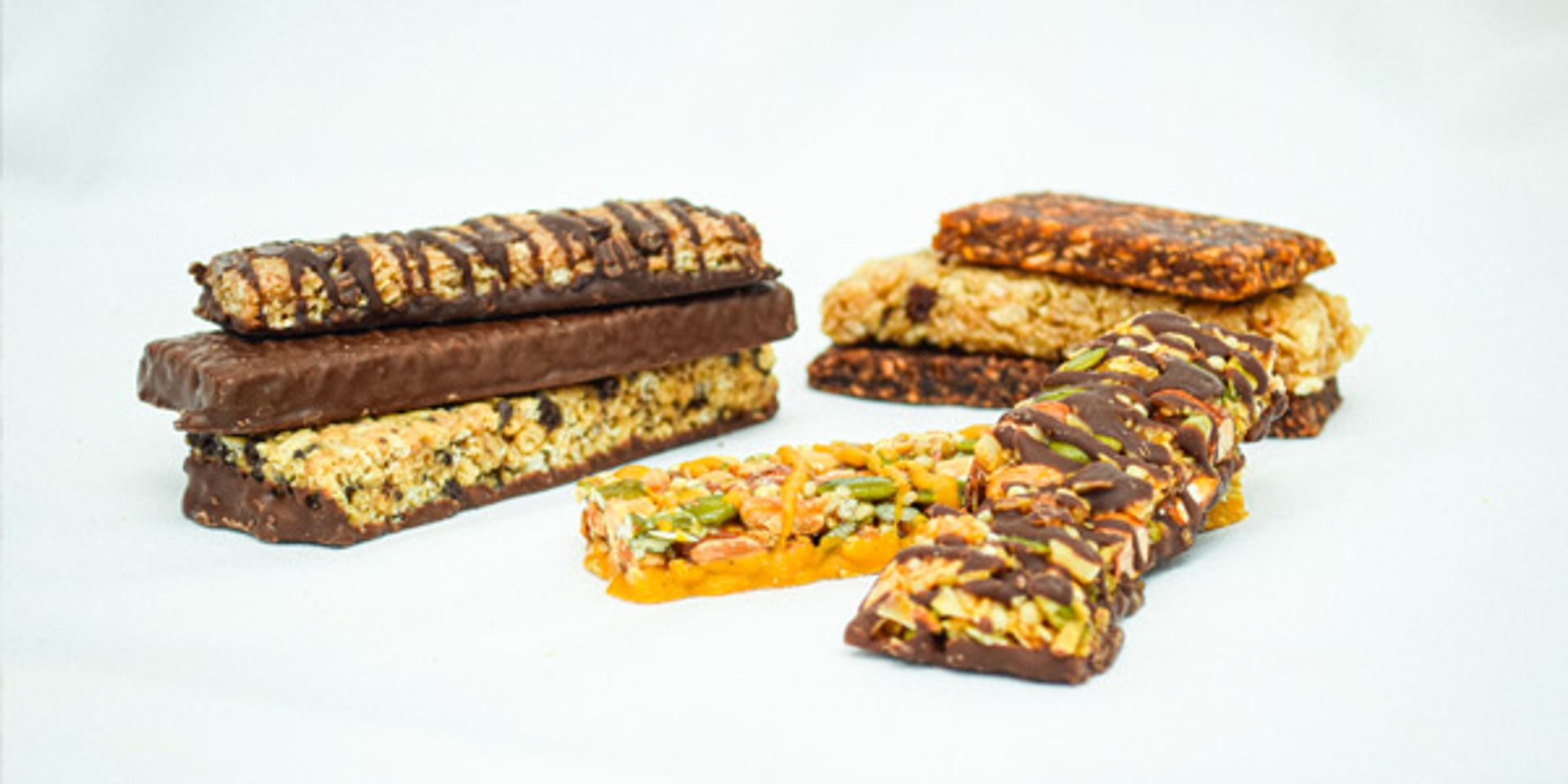
Slab Bar Line
Our slab forming process is typically used for granola and cereal-type bars, or anytime the objective is a less dense product where the desired effect is keeping whole particulates, such as nuts or grains intact. The product is first gently compressed beneath a series of rollers over a conveyor belt. The resulting slab is then cooled and cut into bars to any specified width or length. If enrobed or drizzled with coating, the bars will pass through an enrober and a second cooling tunnel before being individually wrapped.
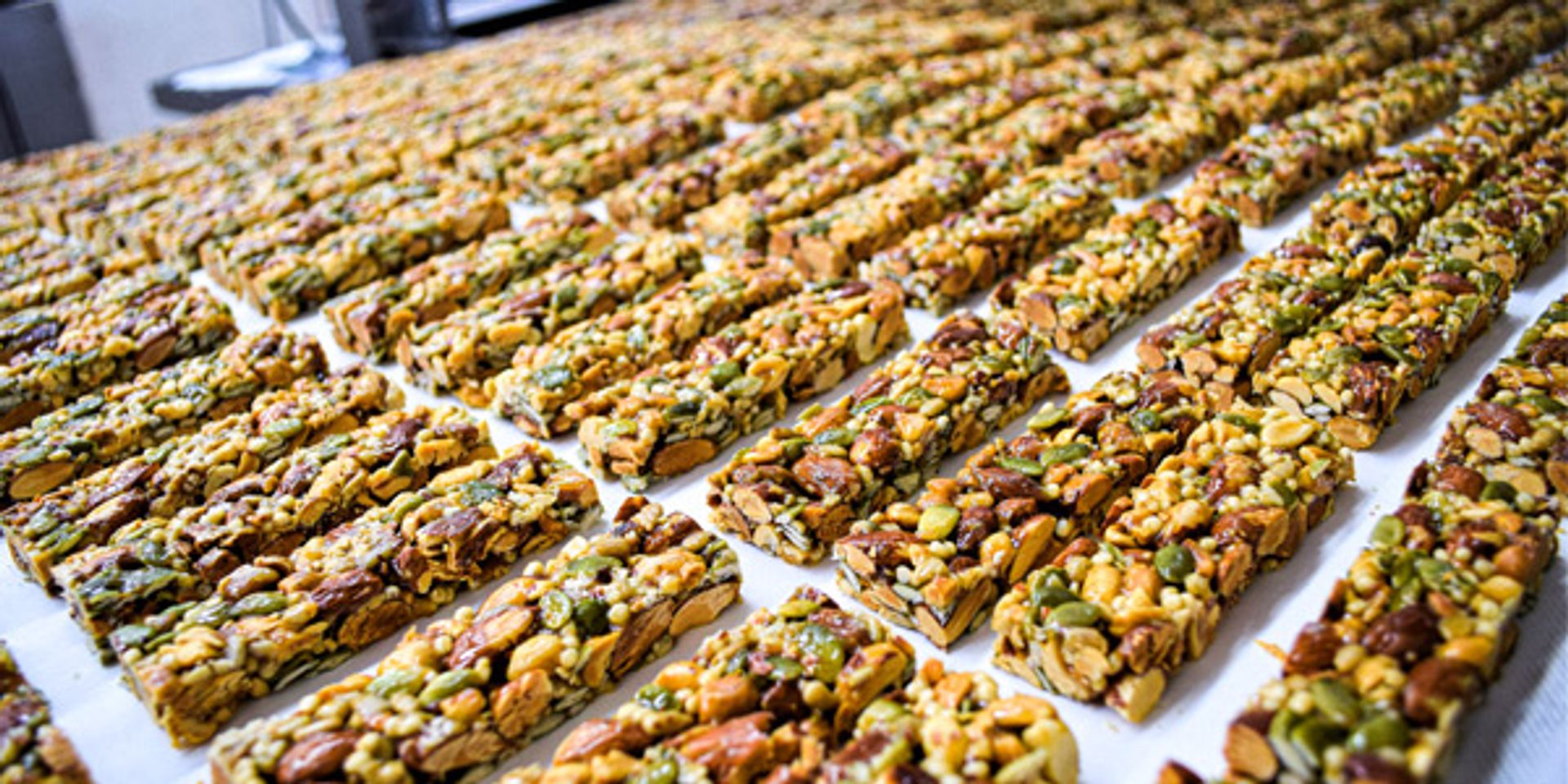
Layering and Depositing
Layering with caramel, fudge, fruit paste or other viscous material can be done on either the Slab line or the Extrusion line. Depositing is conducted on the Slab line where metered amounts of particulates such as nuts, chocolate chips, fruit or candy pieces are applied to the slab from above as it travels on the conveyor.
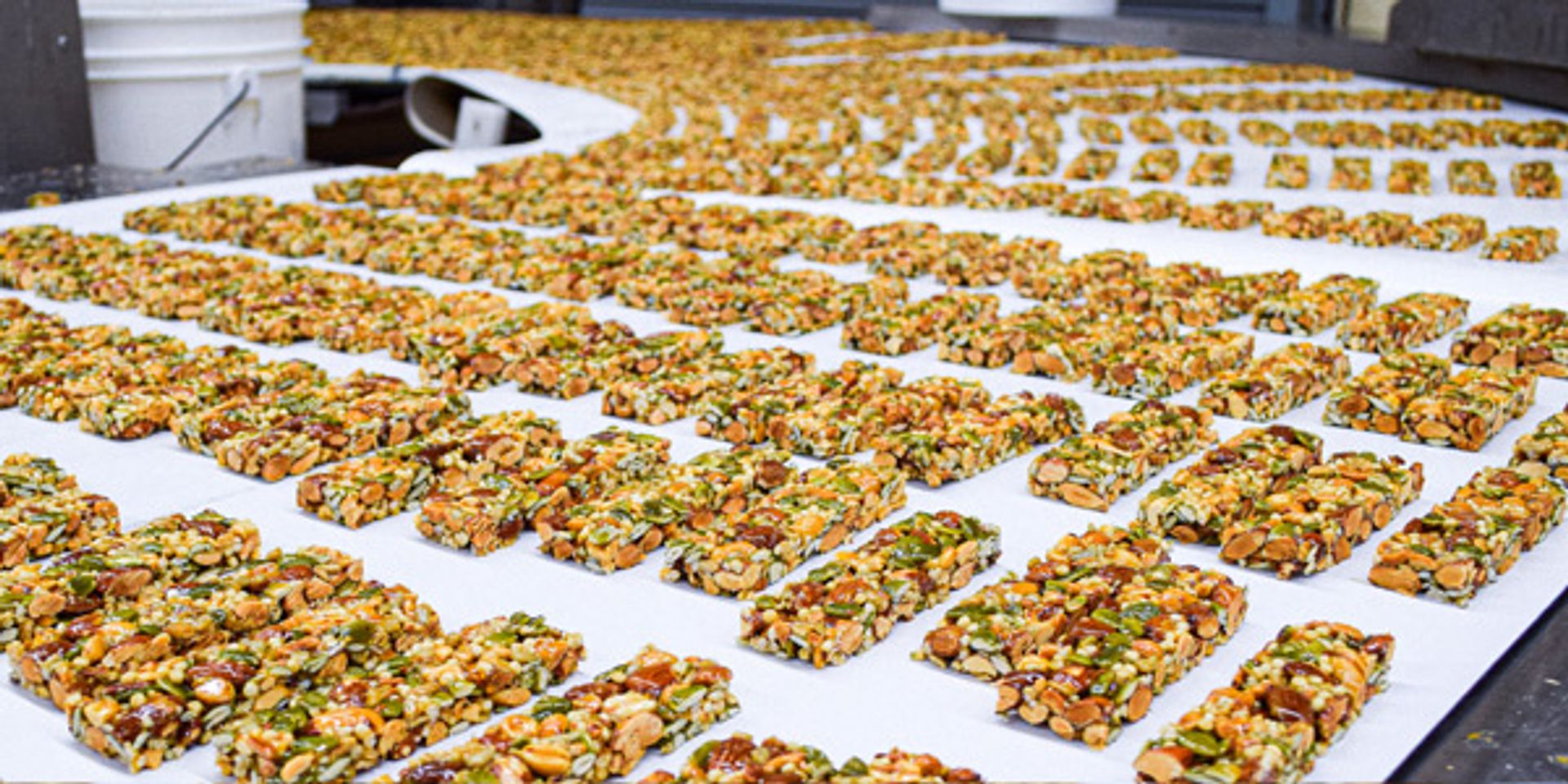
Wrapping & Packaging
- All produced bars are individually wrapped by one of several specialty wrapping machines. A product lot code is applied by ink jet to each individually wrapped bar.
- Sealed and wrapped bars are then packed into cartons by an automated packaging system.
- Each carton is erected, loaded and sealed with a printed lot code typically identical to that of the lot code printed on each of the individually wrapped bars.
- Packaged cartons are then conveyed through an automated check-weighing system. In the unlikely event any cartons are mispacked, they are automatically identified and rejected by the system.
- Finished cartons are then conveyed into an automatic case packer where they are assembled into a pre-programmed configuration prior to being loaded into a corrugated master case.
- Once sealed the case is coded, palletized, and readied for shipment.
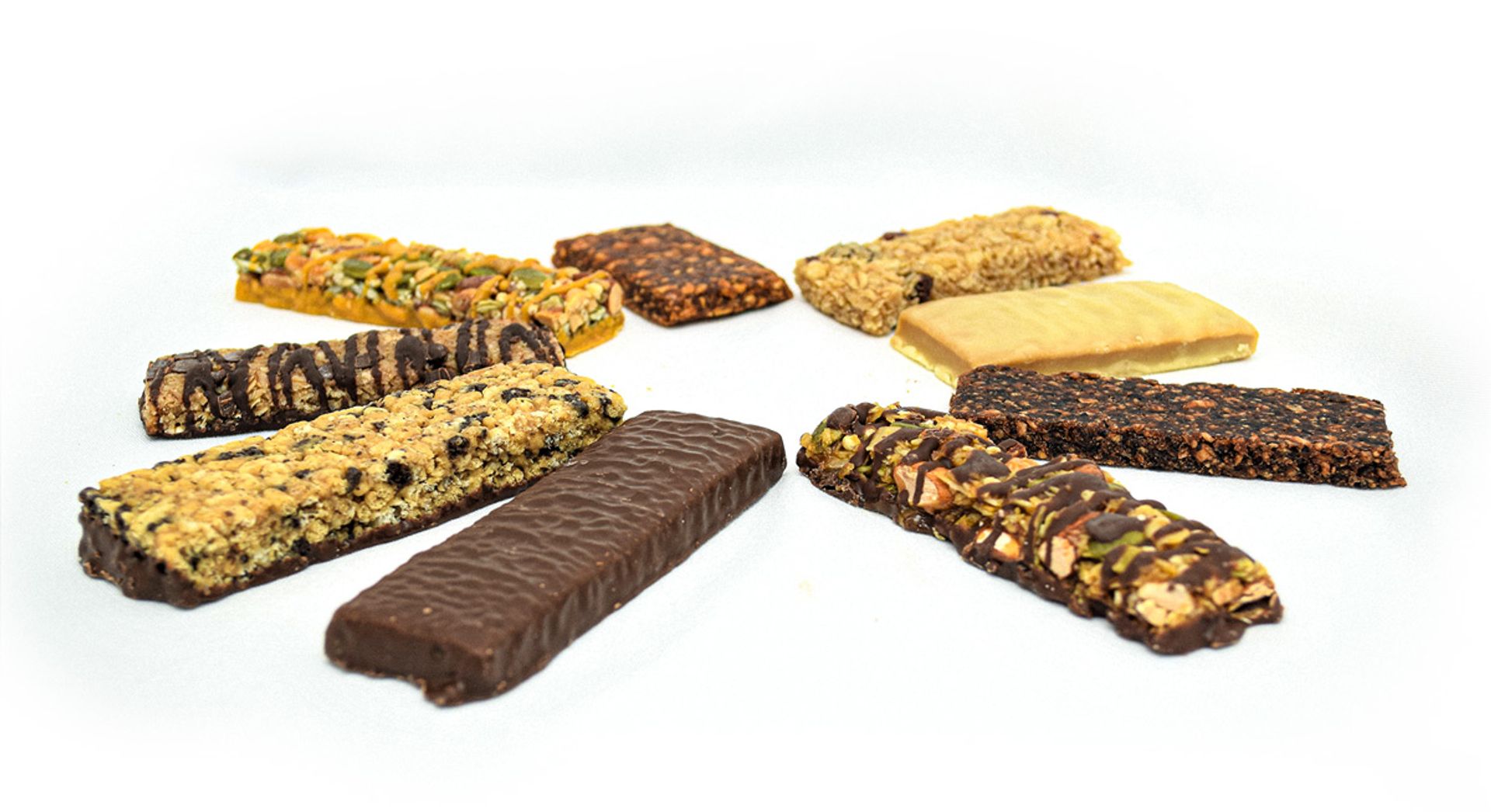
Let's Get Rolling!
Let’s talk about your goals, needs and product production challenges.